As part of a long-term partnership with the KANSAI HELIOS group, our company Kolektor Sisteh has established a comparable level of digitization in the majority of plants in the field of production process management, and thus helped to increase their productivity and quality
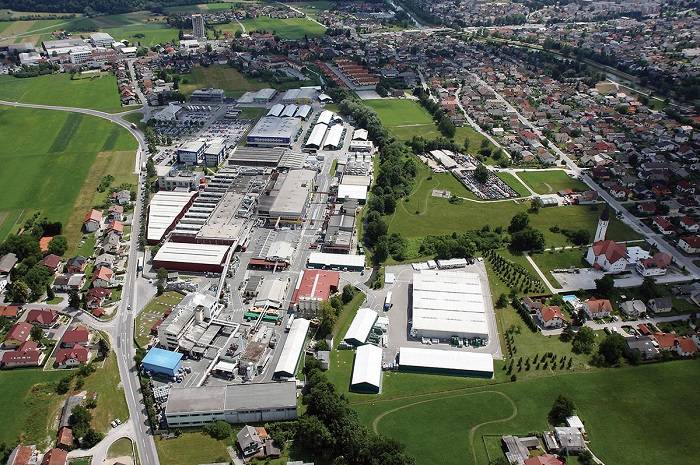
Podjetje Helios TBLUS (factory of paints, varnishes and artificial resins) represents the European center for the development of the KANSAI HELIOS Group and is also the largest company in the Group. It was founded in 1924. Today, it operates with production units at three locations: Količevo, Preska and Črnuče.
Due to the dynamic nature of work, they were facing daily challenges in production planning in the past, such as:
- time-consuming updates of Excel files;
- mismatched data in the ERP system;
- continuous coordination of shipment dates;
- demanding coordination of delayed dates of deliveries to customers;
- never-ending coordination of priorities between individual plants and planners.
Dynamic production scheduling and recipe management
Introduction of dynamic scheduling, which is one of the functionalities of Sinapro modular solution, boosted efficiency of their processes. Among other things, the solution enabled the following:
- review of the actual occupancy of individual resources;
- scheduling of production taking into account the normative times of individual operations;
- insights into the actual progress of a specific work order;
- automatic delays of successive technological operations/work orders in case of unplanned downtimes;
- automatic updating of data in the ERP system according to the actual progress of work orders;
- automatic consideration of non-working hours when scheduling work orders;
- prioritization of selected work orders in terms of deadlines in case of plan changes.
Dynamic scheduling was considered a quality foundation for further projects of production process digitalization. Given the nature of the process industry, the introduction of SinaproBatch recipe management system was among the most important ones as it provided them with many advantages compared to the manufacturing method they used previously. The system enabled them to:
- reduce production times and increase production capacity;
- increase reproducibility and reduce the number of errors;
- increase adaptability and speed of response to the changes in the technological process which are becoming very frequent: recipe adjustments due to changes, availability and quality of raw materials.
Paperless production for real-time reporting
As part of the comprehensive and gradual digitization, the KANSAI HELIOS group achieved the standard of paperless production with the introduction of Sinapro system, which means that, in addition to work orders, all other documents that were previously used in physical forms, were digitized. Thus, they also achieved high level of traceability, which, in combination with the digitization of control procedures, ensured high level of quality.
Digitization of maintenance along with the advanced notification system further contributes to the reduction of unplanned downtimes, as maintenance personnel are automatically notified via mobile phones in case of downtimes; in addition, the execution of maintenance interventions at individual workplaces is carefully recorded in digital form, which ensures transparent intervention statistics and thus enables wide possibilities for continuous improvement.
The advanced reporting system, which also represents one of the functional components of the Sinapro system, offers a real-time overview of the actual state of production processes and a simplified insight into the causes of potential deviations. In order to increase the transparency of processes, a display of production floor plan was introduced with colored graphs showing the actual state of individual workplaces.
A modular approach in the industrial digital transformation
Thanks to numerous process optimizations and positive user experience of Helios TBLUS company, we were able to continue with the introduction of Sinapro system and good practice in other companies of the KANSAI HELIOS Group located abroad (mainly in Austria, Italy and Serbia). The modular structure of the solution enabled us to gradually introduce selected functionalities, which corresponded to the actual level of digital maturity. Thus, we ensured gradual digital progress, which represented the optimal ratio between investments and added value, or the shortest return on investment (ROI).
At Kolektor Sisteh, we are proud of the trust we have established with KANSAI HELIOS group, which has been using our advanced solutions in the field of automation and digitization of production processes for many years. Experienced project teams and future-oriented management of the KANSAI HELIOS Group are the main foundation of success and successful partnership. Their commitment to achieve the objectives of Industry 4.0 is demonstrated through their constant progress and never-ending digital growth, which also directly contributes to improved business results.
Image Source: KANSAI HELIOS
Back